How to Avoid Costly Shipping Errors with Integrated Shipping and Receiving Software
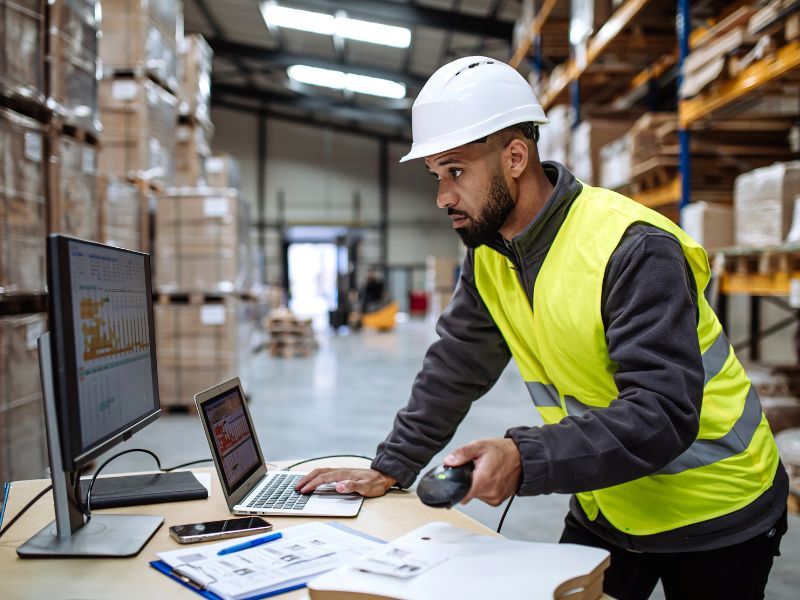
Keep Your Packages on Track Without the Backtrack
Are shipping errors constantly tripping up your business? Have you had customers frustrated by incorrect deliveries or late packages?
In this post, you’ll learn how integrated shipping and receiving software can help you streamline your shipping process and minimize costly mistakes.
By the end, you’ll be equipped with simple yet powerful ways to improve your accuracy, speed, and customer satisfaction using smart automation tools.
Improving Accuracy In Shipping Processes
Address Verification Systems
One of the most common causes of failed deliveries is incorrect or incomplete addresses.
Integrated shipping and receiving software automatically checks customer addresses against carrier databases before the package is sent. This step in the shipping process ensures that businesses reduce errors and get packages to the right door faster.
The impact is significant: fewer returned shipments and more satisfied customers.
By automating repetitive tasks like address verification, businesses save time and minimize waste.
Automated Data Handling
Manual data entry is prone to errors, whether it’s incorrect addresses or product details.
Integrated shipping software eliminates these problems by pulling order information directly from your system and automating tasks like label generation, duty calculation, and order fulfillment.
This automation reduces human involvement in key warehouse processes, helping businesses increase efficiency, cut labor costs, and improve order accuracy.
Preventing Stockouts With Inventory Management
Real-Time Inventory Visibility
Inventory control is essential for preventing stockouts that frustrate customers and slow down the fulfillment process.
Integrated shipping software provides real-time visibility into inventory levels, automatically updating stock as orders are placed.
This keeps your warehouse running smoothly and ensures that products are always available when needed, maximizing throughput and minimizing waste.
Automated Replenishment
By using automated storage systems, you can trigger reorders when inventory levels fall below a set threshold. This automation ensures that your business won’t experience unexpected delays due to stockouts.
With an integrated warehouse management system in place, you can seamlessly manage inventory replenishment, which increases productivity and keeps customers happy.
Reducing Picking And Packing Errors
Barcode Scanning In Picking And Packing
Errors during the picking, packing, and shipping stages can lead to costly returns and frustrated customers.
With mobile devices and barcode scanning technology, businesses can significantly reduce errors. By scanning items at multiple stages—during picking, packing, and shipping—the chances of picking the wrong item are minimized.
This automation helps businesses save money and improve customer satisfaction by ensuring the right products are sent every time.
Storage Optimization With Warehouse Management Systems (WMS)
One of the key functions of warehouse management systems is to optimize storage layout.
By analyzing data on product movement and shipping patterns, WMS can help businesses position frequently shipped items in the best locations. This reduces the time it takes to pick and pack items, increasing efficiency and reducing shipping errors.
Optimizing storage locations also enhances overall warehouse productivity by improving workflow and minimizing mistakes.
Automated Shipping Rule Systems
Shipping Rules And Courier Selection
Choosing the wrong courier or service level can lead to delays, extra shipping costs, and unhappy customers.
With automated shipping rule systems, businesses can set up predefined rules that automatically select the best carriers based on shipment weight, size, and destination. This automation helps businesses reduce waste, streamline operations, and ensure deliveries arrive on time.
By using automated rate shopping, businesses can also compare shipping rates from various carriers, ensuring they get the best value.
Shipment Visibility And Tracking
Real-Time Tracking For Customers
A lack of real-time shipment visibility can leave both businesses and customers in the dark about the status of their orders.
Integrated shipping software provides real-time tracking, allowing businesses and customers to monitor packages from pickup to delivery. This level of visibility reduces the number of customer inquiries and boosts customer satisfaction.
Proactive communication, paired with real-time tracking, keeps everyone informed and reduces frustration on all sides.
Data-Driven Insights And Analytics
Error Reporting And Analysis
Integrated shipping systems don’t just help streamline processes; they also provide critical data insights. By tracking shipping errors and analyzing data trends, businesses can identify operational inefficiencies and take corrective action. Automated reporting allows companies to make data-driven decisions that improve the overall shipping process, reduce costs, and increase efficiency.
Performance Reporting And Carrier Optimization
Shipping software can analyze carrier performance by tracking shipment times, delays, and costs. By using this data, businesses can switch to more reliable carriers or negotiate better rates.
Carrier optimization ensures that the most efficient way to get a package from point A to point B is always chosen, reducing costs and improving delivery speed. These insights help save money and contribute to a better shipping strategy.
Avoid Shipping Errors With Lineage’s Help
With Lineage Accelerate, your business can streamline its shipping and receiving operations, reducing errors and saving money with advanced shipping management solutions. Whether it’s optimizing your warehouse processes or automating repetitive tasks, Lineage offers the tools you need to improve operational efficiency and increase customer satisfaction.
Ready to take control of your shipping process? Fill out our contact form today or give us a call, and let’s get started on making your shipping operations more efficient and error-free